Laser metal deposition - Basics
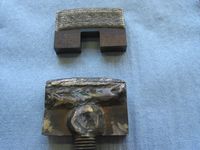
Deposit welding
In deposit welding, precisely placed weld beads are welded on, in order to apply metallic material. The main fields of application are the repair of worn parts and also for parts which have been incorrectly ground or milled. The process is also used for hard facing for wear protection.
In this respect, a heat source is used to generate a molten bath, which is then supplied with a filler material, usually in wire form. Electrical processes such as WIG/MIG or autogenous welding and cladding are conventionally used.
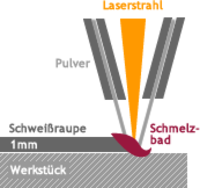
Laser metal deposition
In laser metal deposition, also referred to as laser coating or laser generating, powdered material is welded onto a workpiece, so that bonded, elevated tracks (welding beads) form. In addition to this, the workpiece material is slightly melted at the focal spot of a laser beam.
At the same time, filler material is supplied to the molten bath and also melted. The filler material adheres firmly to the workpiece as a result of the laser metal deposition. Laser metal deposition takes place quickly and continuously.
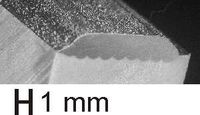
Planar and multilayer coatings can be implemented as required for repair and wear protection by combining the individually welded-on beads.
The greatest advantages of laser metal deposition are provided when the high precision of the laser is utilized and relatively little material with excellent metallurgical properties is to be welded on. The advantages of the laser are negligible in the case of large-area cladding, e.g. in the stone industry, where conventional processes have advantages over laser metal deposition.