Laser hardening - Basics
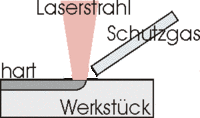
A laser beam is directed over the workpiece in laser hardening, so that a hardened individual track is formed. The material is only heated up locally at the laser focal spot, so that austenitization occurs here. The adjacent material is not touched by the laser beam and therefore remains practically at room temperature. As soon as the heated material is no longer under the laser beam, the heat is very quickly emitted to the surrounding material and martensite is formed (self-quenching).
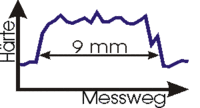
The self-quenching is much quicker than can be achieved with any cooling medium. Both high hardnesses and the freedom from cracks are provided by this type of quenching. The low heat input means that the deformation is also low. It is possible that large hardened components are not deformed at all.
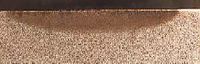
The cross-section of an individual track formed during laser hardening is shown on the left. A typical hardness lense forms. The hardness profiles are also shown. The hardnesses decrease fairly sharply at the track limits
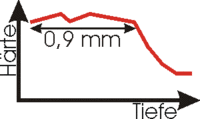
The track width is 9mm and the hardening depth is 0.9mm in the example shown. The hardness ranges from 280HV in the base material to 800HV in the hardened zone.
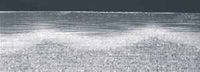
The individual tracks can be combined to form areas by juxtaposing the laser-hardened individual tracks. A cross-section through such an area is shown in the illustration on the left (51 CrV 4). However, a decrease in the hardness may occur in the overlap region.
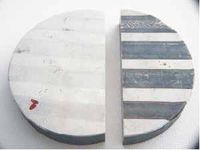
Oxidation of the surface can be prevented in laser hardening by feeding protective gas. Since the local heat input also guarantees freedom from deformation or minimal deformation of the workpiece, no reworking is needed in this case.
Hardened tracks with and without protective gas are shown in the illustration on the left.